- Optimizing Operations
- blog
Discover the best use-case scenarios for Autonomous Mobile Robots
Don't know how to use autonomous mobile robots in logistics and manufacturing? Find out which are the most common use cases.
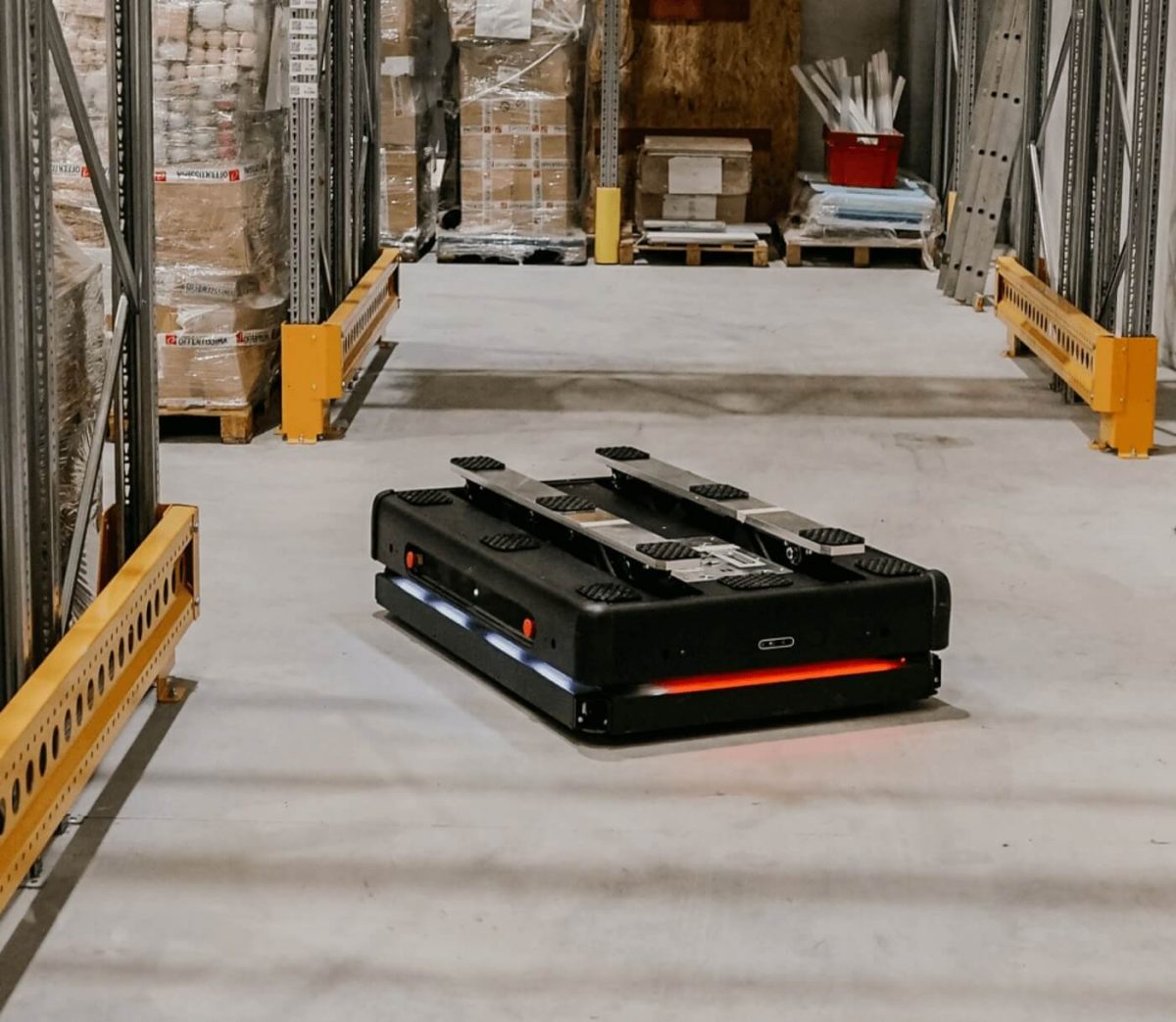
/