- Leading with innovation
- blog
Six reasons behind the logistics robot boom
“Never seen anything like it” is how a researcher describes the “exploding” market of autonomous mobile robots that are taking over warehouses by storm
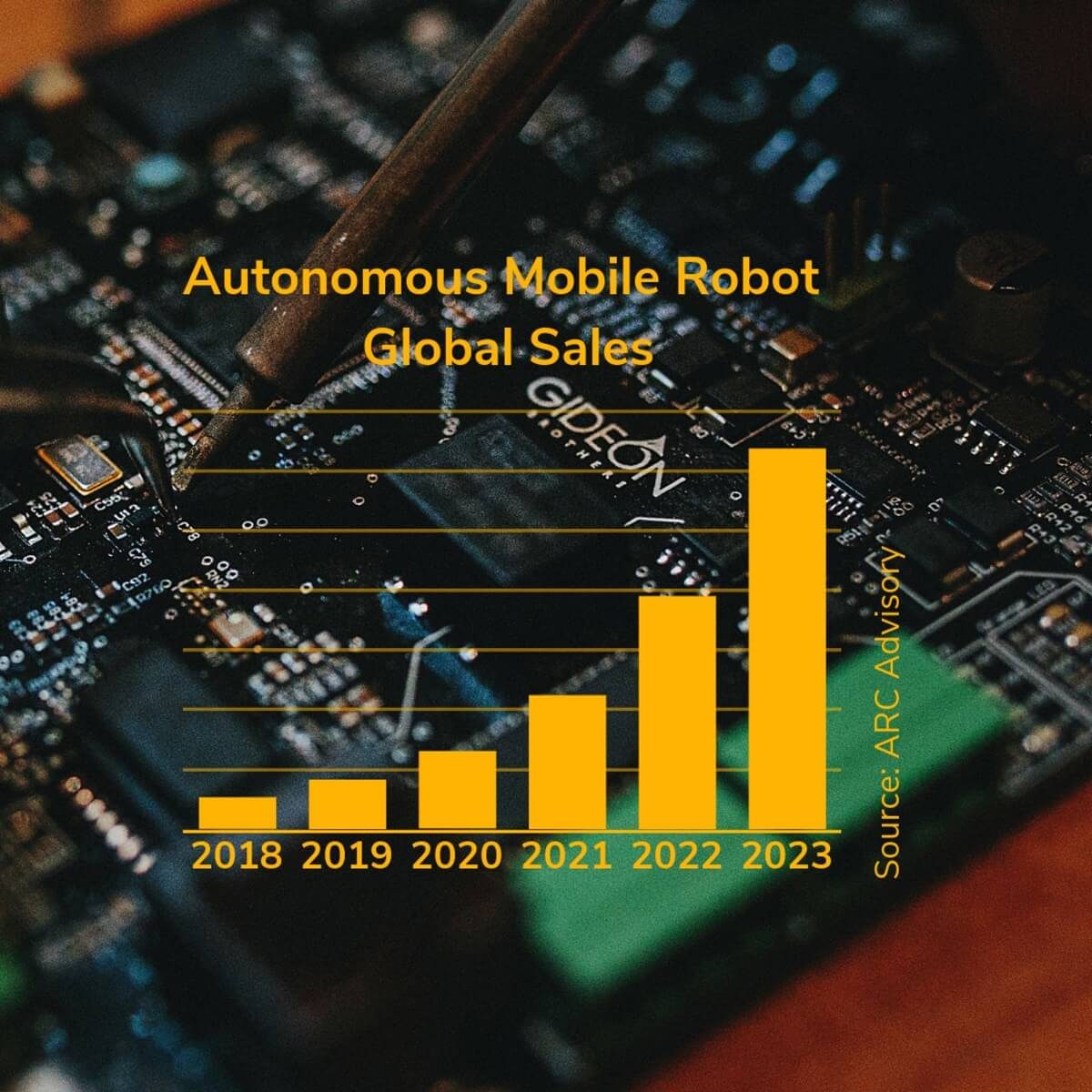
/