- Optimizing Operations
- blog
How to find the best logistics robot
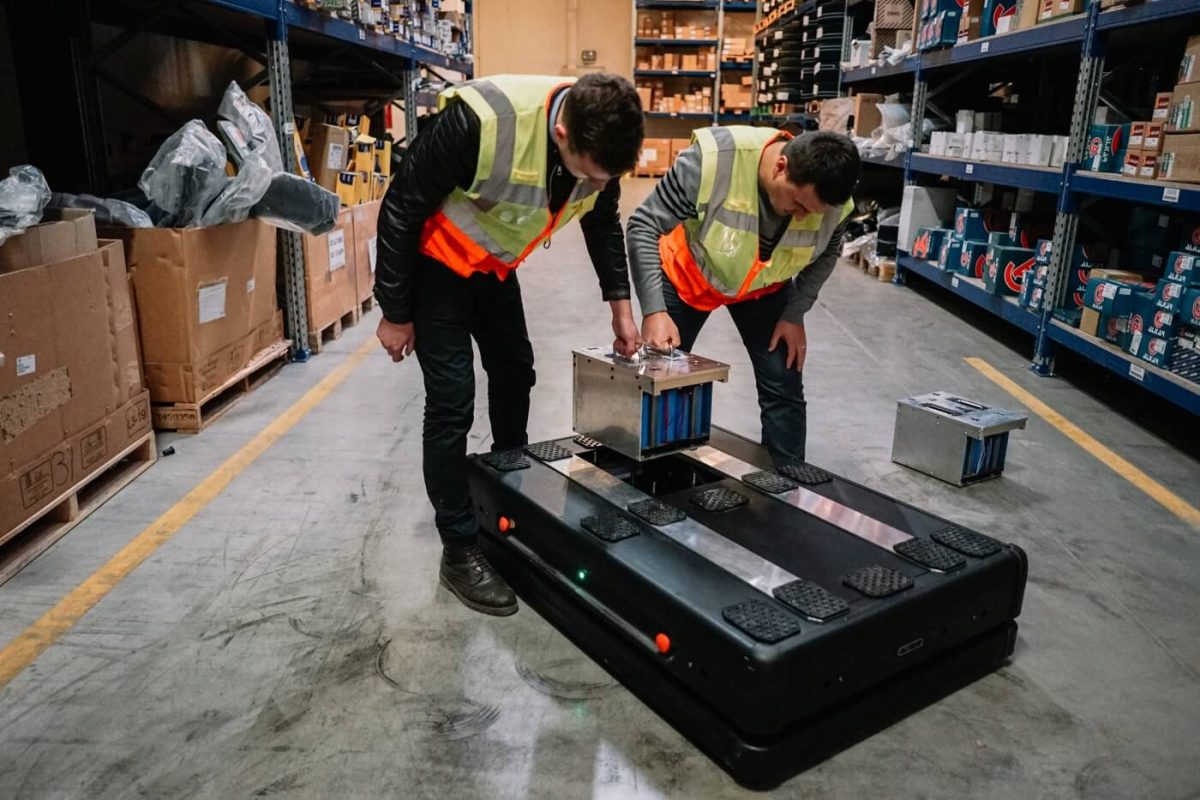
Autonomous mobile robots (AMRs) are a new breed of machines, taking over warehouses and manufacturing facilities by storm. Roll-outs of these collaborative machines picked up considerably around 2015, and the market is now powering quickly through the early adopter phase to enter the early majority phase. Analysts speak of turning points and rarely seen growth rates.
However, the surge in demand for this new technology means that companies now face multiple options. Even when options appear comparable, they may not be technologically or functionally equivalent. Meanwhile, few companies have staff familiar enough with the technological differences and the advantages and disadvantages of each system from looking at a specs sheet. It is difficult to know even what to ask your supplier to avoid unknown pitfalls.
With that in mind, we compiled a list of questions to ask potential suppliers that will help you find the solution best suited for your operations. We also explained why the information is relevant and how it will allow you to make an informed decision.
Useful terms:
Autonomous = Requiring no direct human operator or guidance system, self-driving.
Collaborative = Designed to navigate and work safely with and around people as well as fixed and mobile equipment.
Mobile = Designed to move around facilities, not stationary.
Autonomous Mobile Robot (AMR) = Fully autonomous and designed to navigate itself around people, equipment, and obstacles. AMRs must have simultaneous localization and mapping (SLAM) capabilities as well as autonomous navigation (path planning). Most AMRs on the market rely on LiDAR.
Navigation-related Questions
How does the navigation work?
To be able to do the intended job, your machine needs to navigate around your facilities without help from human operators. There are two ways to do that: autonomy and guidance systems.
If the robot needs a guidance system, it is an AGV (Automated Guided Vehicle) – which means that it will need beacons, magnetic tapes or other systems of virtual ‘tracks’ to follow. Some AGVs will stop if there is an obstacle in their path. While the guidance system is invisible, the machine is unable to move without it or plan a new path (in the presence of obstacles), and therefore the system remains inflexible.
On the other hand, when machines are fully autonomous, they are capable of reconstructing their environment from sensor data and know precisely where they are at all times. These robots are able to recognize changes to their environment, choose optimal routes and navigate around fixed and moving obstacles and persons.
Both technologies – autonomous robots and AGVs – will need onboard sensors: the former for navigation and security and AGVs just for safety. Sensor arrays usually include LiDAR (Light Detection And Ranging) and sonar.
Gideon Brothers offers a new genre of autonomous navigation, based not on LiDAR, but on stereoscopic cameras. Only two other companies offer similar approaches to navigation at this time time. Vision-based (as opposed to LiDAR-based) perception provides a broader range of use cases. For example, such machines can operate in unstructured environments such as warehouses without shelving where the view of background is the only way to pinpoint the location.
Visual perception is also data-rich, offering the possibility of not only sensing the environment but recognizing what that environment holds. Client-specific applications are possible, such as reading bar codes or inventory of client-specific objects.
Useful terms:
AGVs or AGV robots = Automated Guided Vehicles (AGVs). Machines that lack full autonomy, relying on guidance systems such as beacons or magnetic tapes to navigate. AGVs have pre-determined paths (“virtual tracks”). They are a slightly more flexible version of the conveyor belt and are not always designed to work safely around humans (such as the case with Kiva robots). AGVs require more time to deploy than autonomous solutions because of their infrastructure requirements. AGVs cannot travel beyond the path that is planned for them. When these robots encounter obstacles, they are not equipped to do anything other than stop and wait until the obstacle is cleared away.
LiDAR = Light Detection And Ranging. LiDAR is a laser radar that allows the machine to sense its surroundings. It is the standard sensor in industrial AMRs. Its limitation is that it can’t detect low lying obstacles and does not perform consistently in highly-dynamic constantly-changing environments.
Visual Perception (in robots) = Perception based on sensor inputs that arrive from cameras rather than via LiDAR. When used for navigation, vision-based robots not only perform better than LiDAR-based robots but do so across a more extensive range of use cases. Vision-based robots can be used in unstructured, highly dynamic environments (bustling areas with few fixed points). They can detect low-lying and negative obstacles better that LiDAR. Also, unlike LiDAR, cameras provide rich data that can be used for a variety of ancillary purposes (such as security).
Semantic understanding = The capability of an AI-powered robot to perceive objects around it plus recognize and understand what objects are. The process is similar to how humans see/identify objects. A robot equipped with AI- and deep learning-based semantic understanding can recognize people, pallets – empty or loaded – forklifts, carts, load types, bar codes – anything that the robot will need to know for safe operation.
Semantic understanding is achieved by exposing the autonomy technology to large data-sets, comprised of tens of thousands of images. The objects in the pictures are painstakingly outlined using specialized software (or if you’re lucky – AI); each object in the picture assigned a name. The vast exposure to a variety of objects within a class equips robots with the ability to extrapolate that knowledge to new settings.
How are facilities maps created?
The robot – if fully autonomous – creates and updates its own facilities map if equipped with a Simultaneous Localization and Mapping engine (see more below).
Additional details that could be added to the map may include virtual walls, parking spaces and other designated areas, areas of congestion, drop-off and pick-up locations, and other information. Knowing how exactly this process works will help you determine how well the technology solution fits your organization, workflow, and staff capacities.
Useful terms:
SLAM (engine) = Simultaneous Localization and Mapping refers to the complex capability of a robot to build (or update) a map while at the same time keeping track of its own location on the map.
Engine = An umbrella term for a complex component of software. A robot’s autonomy technology consists of several ‘engines’ working together.
Traversability Map = A visual representation of the level confidence that the robot has in its ability to pass safely through an area – it answers the question – can the floor space be traversed based on various factors such as the presence of obstacles, holes, etc. Fully autonomous robots construct their map based on sensor inputs.
What happens if there is an obstacle on the route? What if the robot enters a busy area?
An autonomous robot should be able to move around the obstacle and/or calculate an alternative route, while AGVs are more limited, with some halting entirely until the barrier is removed. Knowing what happens when the robot confronts obstacles vis a vis what you know about your warehouse environment will help you determine if a strict protocol is required in areas where machines will be moving. It will also show whether you need to take into consideration potential idle time due to frequent obstacles, especially in case of human error. Autonomous robot systems may have special features to deal with busy, high-traffic areas allowing more efficient time management.
Will the robot sense low lying or negative obstacles (depressions)? How does it avoid crashing into one?
Only camera-based visual perception can perceive low-lying objects and negative obstacles. Low-lying objects are not visible to LiDAR-based machines, which are the majority of the current crop of logistics robots, because they fall under the LiDAR’s sensing plane (roughly, at the height of your ankle).
The forks of an empty forklift are exactly the kind of obstacle that are invisible to LiDAR. When the forklift is not carrying anything, its forks must be in their lowermost position, in line with safety regulations. As this is a common obstacle in warehouses and manufacturing facilities, some suppliers recommend that an idle forklift always carry an empty pallet, but this can cause an irritating disruption to the workflow.
Another type of obstacle invisible to LiDAR are low platforms – such as bases of shelving pillars that aren’t protected by guards. LiDAR sensors are also unable to see depressions/holes in the floor.
Ask your supplier what they recommend if your warehouse space has such obstacles.
Will the robot be able to navigate in facilities without fixed elements such as racking and shelving infrastructure?
Autonomous robots based only on LiDAR sensors are not able to navigate if there are no fixed points for orientation. However, robots equipped with visual perception will be able to navigate by checking its progress against the background, ceiling and other visual cues.
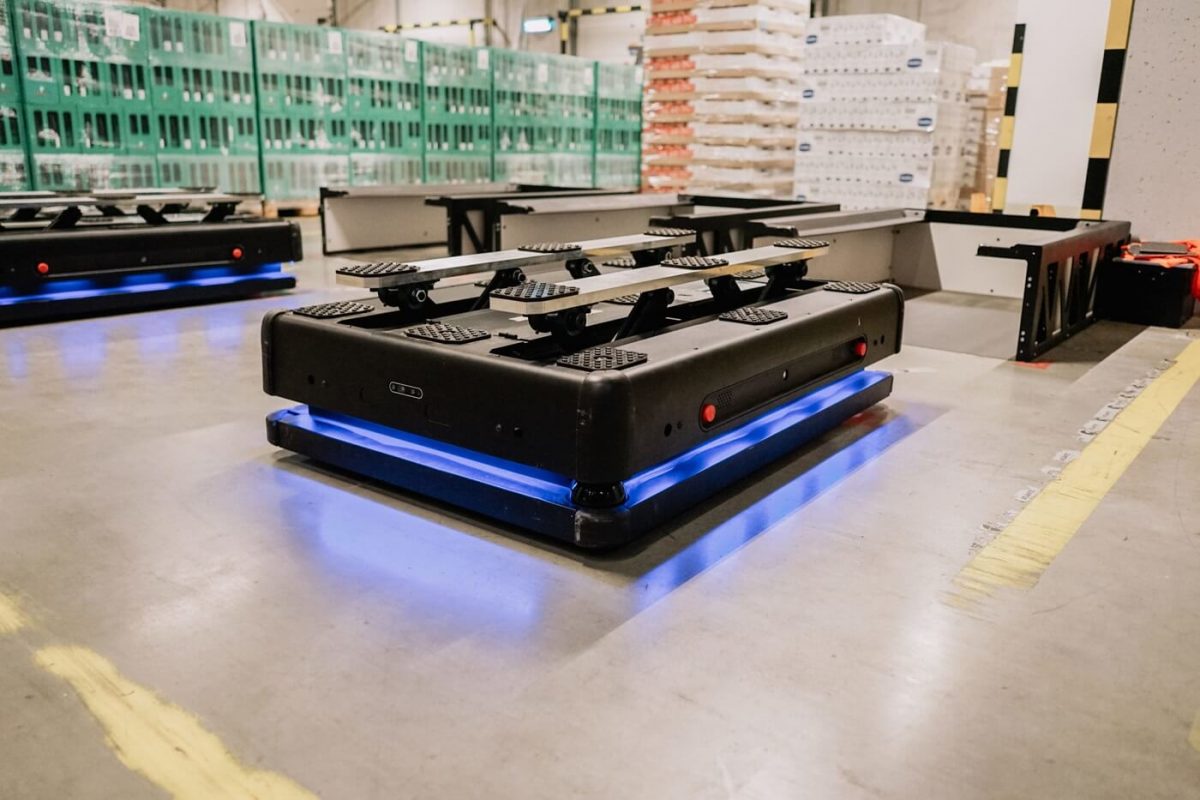
Load and Operation Specs Questions
What is the maximum load? What are the maximum dimensions of the load?
Other than the maximum weight of the load, it is handy to know how wide, deep, and high a load must be. For some solutions, stability and specific center of gravity may be relevant.
Are there any additional components required, such as transport boxes?
Some solutions require that the load is transported in specially designed cages or boxes, or secured by netting or other restraints. A critical question that you should not forget to ask is if the supplier requires that you buy this equipment from them and how much it costs. The dimensions for such boxes will also help you determine how well these fit with your shelving infrastructure.
What is the maximum speed? What is the lifting time?
Knowing the speed will help you calculate the overall usage efficiency as compared to your current operations. In the case of robots and AGVs that lift the load, also ask how long it takes them to perform such operations. Please note that many jurisdictions have security regulations limiting speed. The most common speed limit is 5 km/h (1.39 meters per second or 3.1 miles per hour or, roughly, a walking pace).
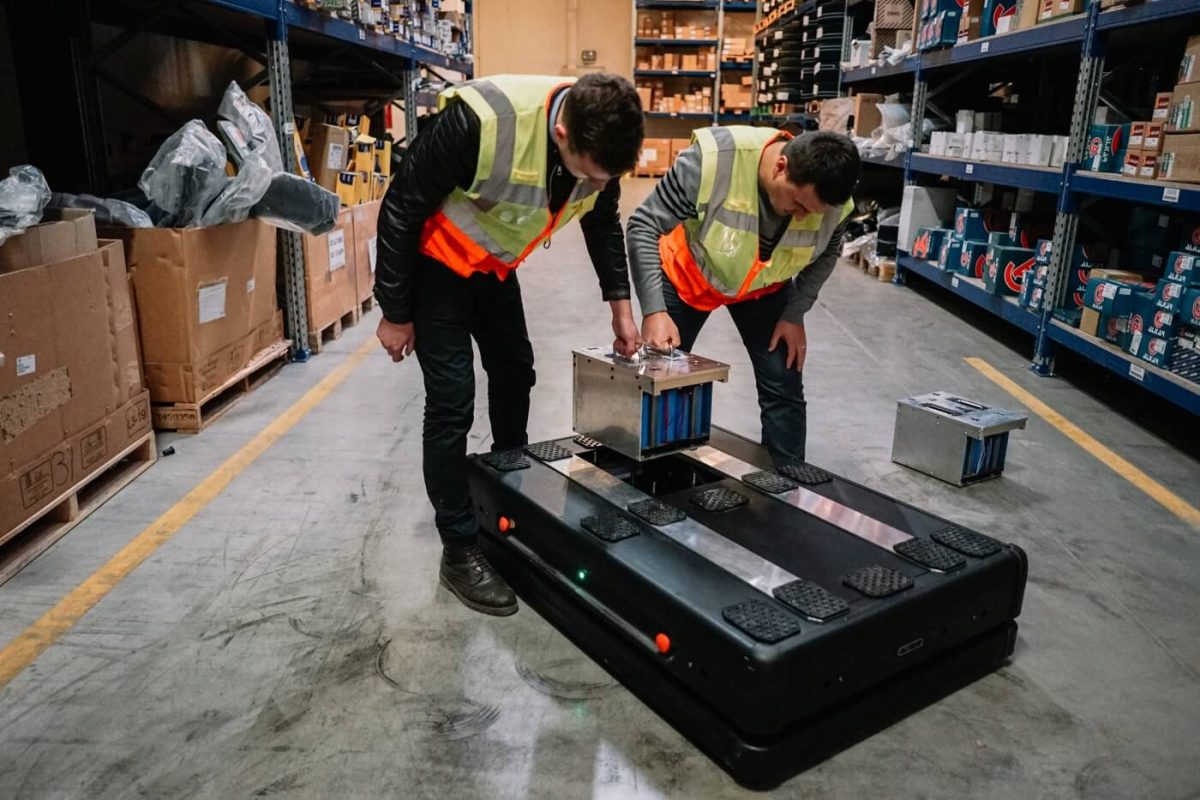
Charging-related Questions
What are the battery specifications?
Relevant battery specs will help you determine costs and energy consumption, both long and short term, plan network loads and calculate efficiency. You should know when you’ll need to replace the battery, how exactly the replacement is handled, and how much it will cost.
What is the charging downtime, and how can it be minimized? How does the charging work?
How long is the single cycle of the battery, i.e., how long can the robot operate before it needs charging? How long does it take to charge – and the robot to sit idle? Is the battery swappable, and if so, how do you need to turn it off for that?
Very few suppliers offer machines with hot-swappable batteries, allowing the battery to be swapped amid operation and thus bringing the downtime to a minimum.
What are the technical requirements for charging stations?
Ask these details to avoid being surprised later if there is small print related to battery charging.
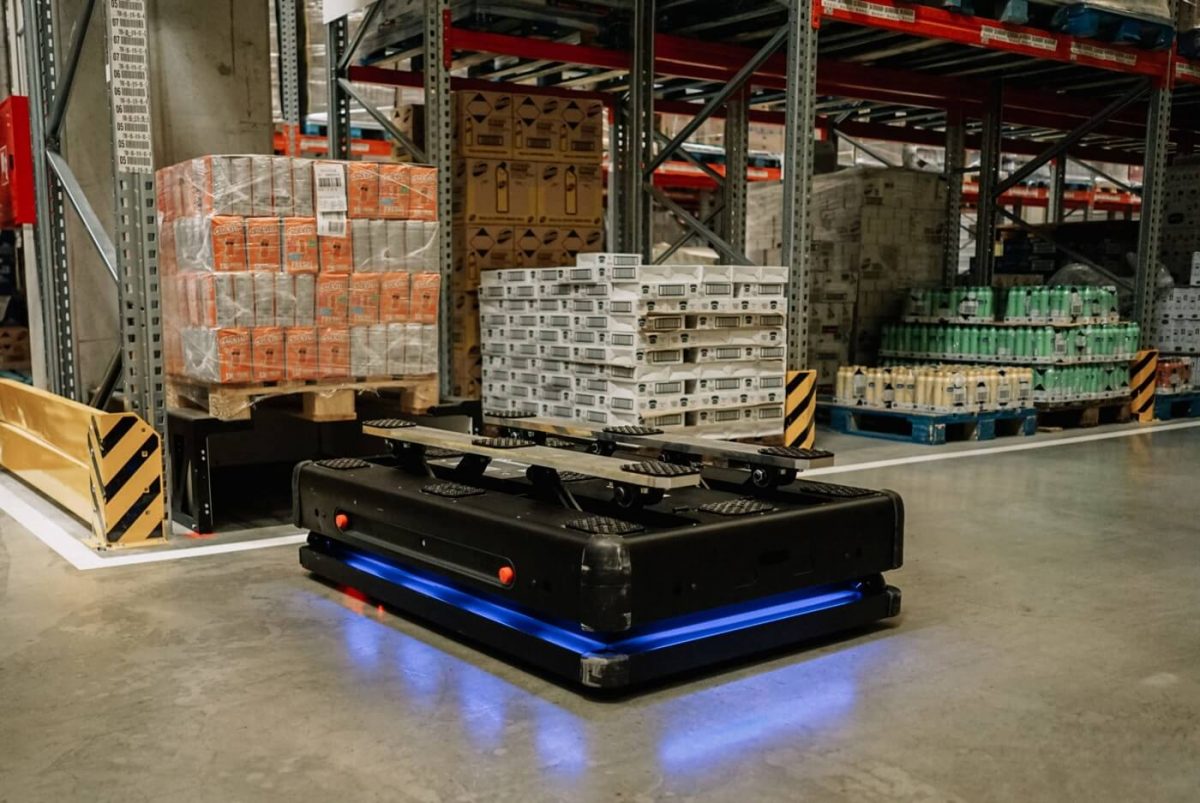
Infrastructure-related Questions
What are the requirements for the condition of the floor?
Industry-standard facilities, where a typical indoor forklift can operate, should also be able to host all robots, but you should still check. Vertical obstacles, incline grades, flooring material, liquid/wetness, and dust, as well as color and floor markings, could all be relevant, depending on the technology.
What are the environmental requirements?
Temperature and humidity may influence the operation of the machine, as well as lighting and shadows. How busy are the facilities, or some of the areas? Will the forklifts and other equipment have to be kept out of the way always, and parked in separate areas?
Also, please be aware that there are robots intended for indoor use and those that are intended for outdoor use (or both).
In what sort of warehouses can robots work?
This depends on the type of robot autonomy. Those using only LiDAR-based navigation can operate only if they can navigate against fixed elements such as shelving. In unstructured, open warehouses, with constantly changing features, navigating against the background is the only option, and this is something only machines with visual (camera-based) perception are able to do.
Is there additional infrastructure or equipment that must be installed?
AGVs will require a guiding system. Other possible infrastructure includes pick-up and drop-off racks or frames, charging stations, special cages used to place the load, particular shelving or other infrastructure.
What is the minimum maneuvering space?
What is the minimum width of the robot’s path/corridor? What is the turning radius? If it lifts the load itself, what is the maneuvering space needed for that?
Which areas must be specially marked or reserved?
Other than drop-off or pick-up zones, specially designated areas might include parking space, charging areas, no-go zones – for example where idle forklifts (not visible to LiDAR-only robots) are parked. Ask your supplier what are the requirements for any of the required areas so that you can plan surface area reallocation if necessary.
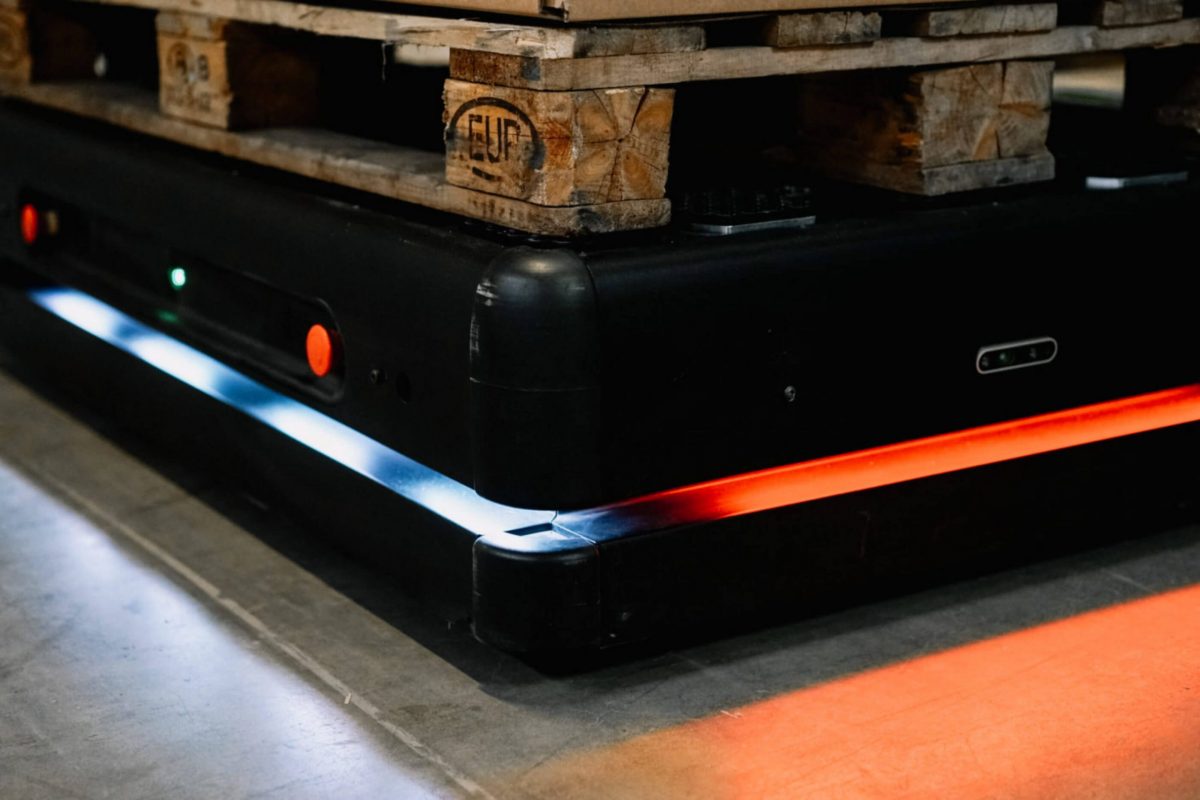
IT infrastructure
What are the requirements for IT infrastructure – WLAN, WMS integration, and server installations?
Do you need WLAN, and if so, what is the recommended bandwidth? Do any of the components need to be installed to the client’s servers? Do you need integration with WMS (Warehouse Management System) software, or are there alternatives for automated task input? Knowing IT requirements will help you determine any investment in network equipment and integration costs.
What is the robot interface? How is the robot operated?
Does the robot have a remote device, or is it operated through a web/tablet/smartphone application? What type of input can be automated and how exactly is a transport order triggered? What should be done by hand? Ask your supplier to describe the process, and this will help you determine how it will best fit into your workflow.
Safety-related Questions
How do the safety features protect humans and infrastructure?
Request a detailed explanation of security features to uncover any risks. Security features should include details on sensors, emergency stop procedures – including all fail-safes and redundancies in the system, sound, and visual warning signals.
Are there use restrictions around forklifts and people?
Some systems may have limits. For example, machines relying only on LiDAR sensors can’t sense low-lying objects such as forks of an idle forklift in their lowermost security mandated position (see above). Also, some robot systems can get bogged down or confused in busy areas. Knowing all restrictions will help you determine the right solution for your facility/ies.
What are the recommendations for risk minimization?
These recommendations will help you determine if any operational and procedural changes to your work environments are necessary. For example, this might include adding floor markings, warning signs for staff, locked areas and virtual walls, etc.
Use Cases and Efficiency Improvements
What are the ideal/possible use case scenarios?
Ask your supplier to provide examples of use cases – real or modeled. Even with all the questions asked and specifications provided, there may be some deciding factor that will make one solution better adapted for your organization, workflow, and facilities. Ask for any reference projects the supplier can present.
What efficiency improvements can be expected?
Ask your supplier to provide more data – real or modeled – on the efficiency gains you can expect. A made-to-measure model, based on your actual operations, would require you to provide a potential supplier with real data. Please note that such an analysis would constitute consulting services that some suppliers may not offer, or would charge separately.
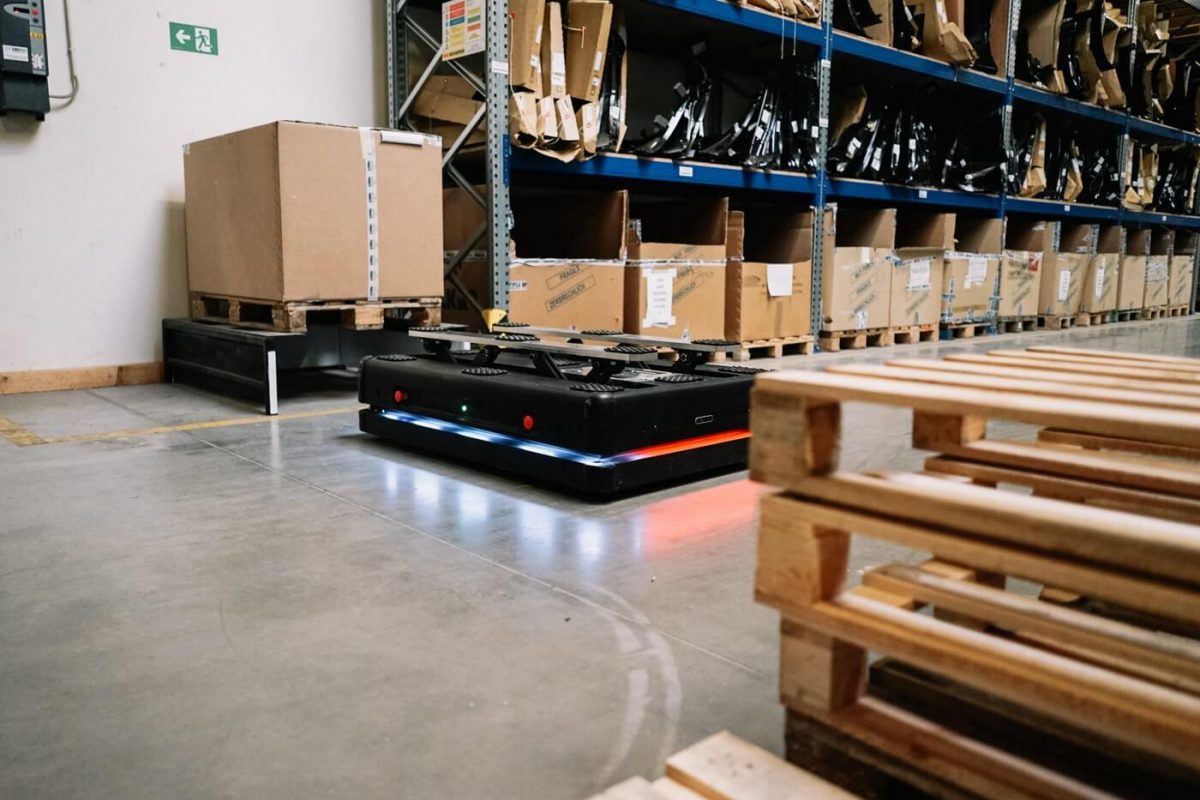
Support-related Questions
How is the support organized during deployment?
Who will deliver and set up the system? Will there be someone from the supplier’s organization on-site during the initial roll-out period? Will someone from the supplier’s organization be consulting the client on implementing the project? Who will provide training for operating the robots as well as maintenance? These questions will help you determine both costs and staff requirements associated with the roll-out.
What constitutes normal wear and tear of the robot?
What parts will need regular changing? What is their expected lifetime and cost? How are these supplied? What are other maintenance recommendations? What is the expected downtime due to maintenance? What are the disposal recommendations? Knowing this will help you determine Total Cost of Ownership as well as ROI for investment into logistics robots.
What are the options regarding finance and insurance?
Do you need to buy the robots and any equipment, or does the supplier offer leasing or Robotics as a Service option? What type of maintenance is covered? What are the insurance options? In the case of acquisition, what are the terms, warranty, maintenance, and other support options? What happens if something goes wrong? Knowing all these details will help you determine the option best suited to your operations.
If you want to know more check out our free e-book that will help you understand when and how to select autonomous mobile robots as your preferred material handling solutions.
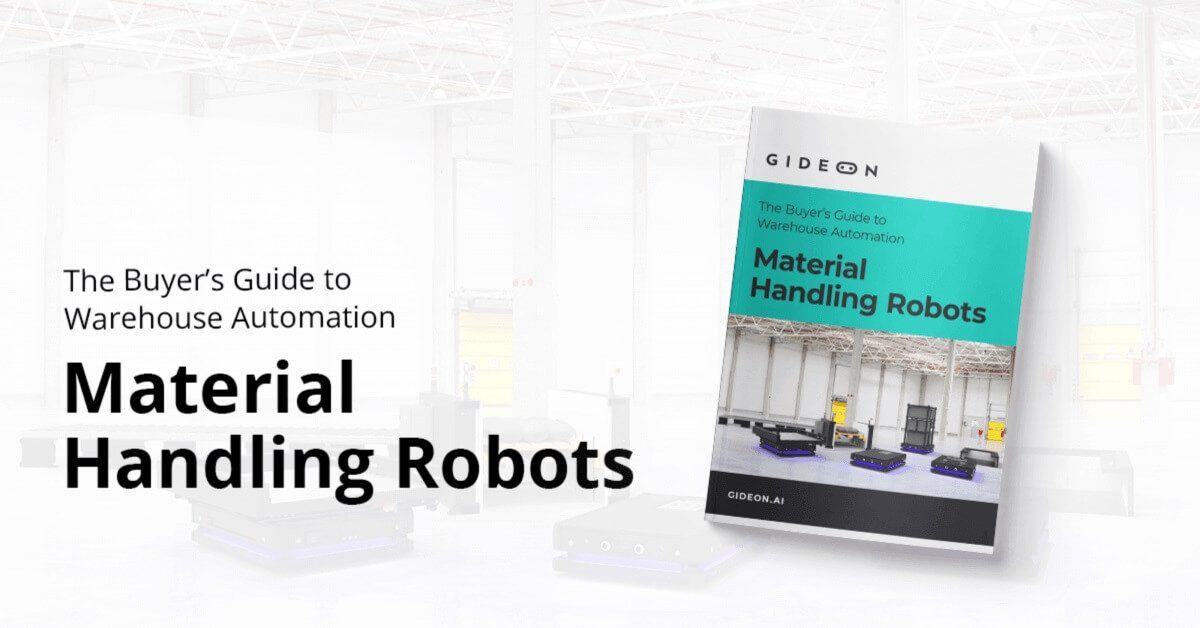