- Building a resilient supply chain
- blog
DB Schenker case study: Autonomous robots in supply chain
Learn how the global logistics leader deployed Gideon Brothers’ pallet handling robots in their 3PL center operating for a prominent German carmaker
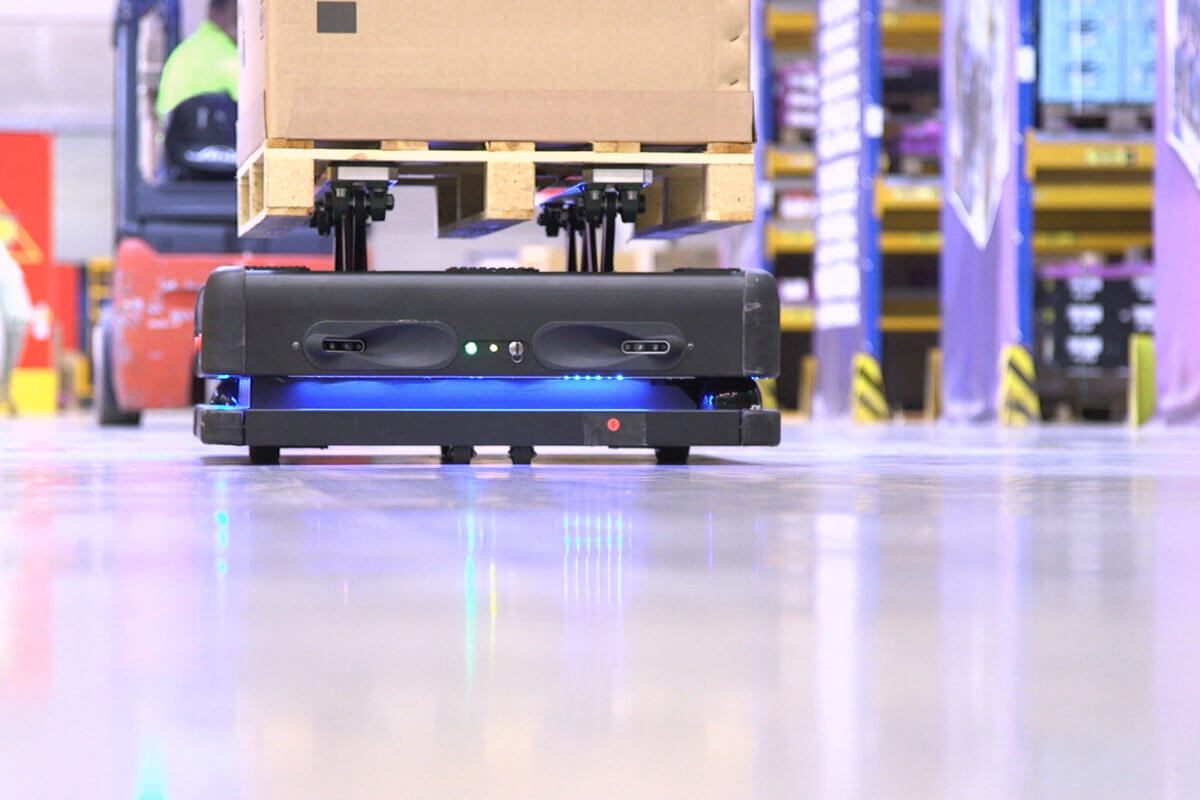
/